Managing Product Lifecycles
for a Sustainable Future
by Patrick Hillberg Ph.D.
In 2013, I created a graduate engineering management course at Oakland University called “Product Lifecycle Management”. It was what an engineer might expect from a PLM course, but over the years has changed dramatically, and a purpose of this blog is to keep past students engaged, as well as anyone else interested.
The OU ISE department now provides many technical courses in PLM, and my course and my interests focus on the business and societal aspects of “Managing Product Lifecycles”. It is much more about organizational learning than PLM technology.
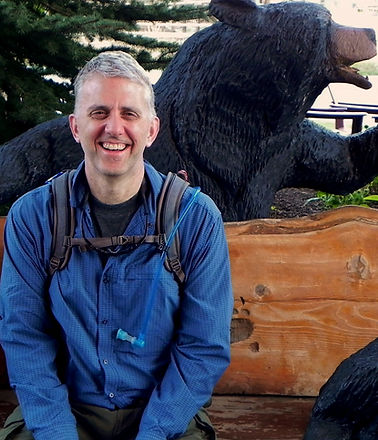
This site includes references to nearly all of the course material, plus other stuff I find interesting but would be too much for a 14-week course. Lecture videos can be found here, as well as my own writing, and links to the writings of others.
Scroll
Other Stuff
For The Digital Enterprise Society (Podcast)
For CGS Advisors
Workforce Development Panel at National Academies
With associates to the National Manufacturing Institutes
Systemic Risk: Systems Thinking, Pandemics, and Climate Change
On 10-Jan-2020 I spoke at a conference, and sat next to someone with "flu-like" symptoms; on 12-Jan I had what I later learned were COVID-19 symptoms, but it was not until 16-Jan that the first known US case of COVID-19 exhibited their first symptoms, and the diagnosis followed about a week later.
It is clear that the SARS-CoV-2 virus infected people throughout the world long before it was recognized, and was already present at this international aerospace conference before anyone in the US knew they had it. Tests were not available until months after my infection had run its course… but that is the point. We have no means of knowing when a novel virus is infecting the world.
I wrote a chapter for the conference proceedings, and in the process researched pandemics, systemic risk, and their obvious connection to climate change. I posit that the manufacturing and economic methods developed in the early 20th century (Industry 2.0) ended in December 2019, as the world faced a long-predicted pandemic of truly world-wide scope. The next decade will decide what the next century will be, but I envision a need to reshore supply chains, increased use of digitalization, and improving the skills of the advanced manufacturing workforce.
The second industrial revolution led to the greatest growth in standards of living and retreats from poverty in the history of humanity, but that growth is now limited by its own success. Cities have expanded into viral reservoirs, and we quickly transport unknown viruses around the world. And as the world warms, new viruses are released from the permafrost, and hurricanes, fires and floods drive humans away from both expanding deserts and rising seas. According to a study by Deloitte, 136 mega-cities across the globe (New York, Miami, Jakarta, Mumbai, …) are at risk due to sea-level rise.
Organizational Learning:
Better Products Need Better Cultures
Scandalous Products…
In April 2014 I consulted with a well-known engineering firm, and by chance the CEO of General Motors testified to Congress that same week about GM's engineering failings which led to over 120 deaths and an Ignition Switch Recall. This event lives in my mind because the engineers at the client firm chose to follow the same failed processes that led to GM’s scandal, in spite of conversation relating the two. (The newly hired quality manager said, “everyone does this – GM got caught.”) It made the point that scandals are not individual events, but the result of organizational norms and pressures. Students in my class discuss the events at GM in an authentic way, in the relative safety of my classroom.
In 2019, the class had grown in size and was researching a number of scandalous products, including the Flint Water Crisis and Volkswagen’s Dieselgate, when the second Boeing 737 Max crashed, due to a flawed automation system known as the MCAS. (Unfortunately, there will always be new scandalous products for a product lifecycle class to study.) Later classes also investigated Toyota’s Sudden Acceleration problems, and the Deepwater Horizon explosion in the Gulf of Mexico, among others.
And Failed Innovations…
Interestingly, one team looked at Blockbuster’s inability to innovate to counter the threat posed by Netflix, and while no lives were lost, certainly Blockbuster’s fortunes were. The organizational norms which allow for scandal also inhibit innovation.
A theme to the class is that
-
Decomposition leads to Dysfunction
-
Dysfunction leads to scandal &/or missed innovations
-
Collective learning is key
In short, if we want better products, we need better product development cultures. Lectures and readings can be found under the Organizational Learning topic.
New Learning for a 4IR Workforce
The new industrial revolution (the 4th) requires vastly different means of learning to develop and maintain a very different workforce. A 2018 study by Deloitte and The Manufacturing Institute showed that by 2028 employers would have 2.4 million skilled manufacturing jobs which could not be filled. If we assume a technical knowledge half-life of five years, 75% of what the 2108 workforce knew will no longer be relevant in 2028.
But the world-wide events beginning January 2020 imply that the 2028 reality is likely worse than the report projected in 2018, on at least two levels:
-
COVID-19 introduced substantial shocks to the global value chain, which first materialized as shortages in masks, personal protective equipment, and ventilators in the United States, and is currently (in May 2021) appearing as unused vaccines in wealthy countries, and rampant infection without inoculation in poorer ones. The global value chain will not recover until the globe is vaccinated, and booster shots will be needed on an annual basis. The nations of the world need to localize their supply chains. (In this, I see value in Digital Twins… we should replace the trade in physical products with trade in virtual products, manufactured local to consumption.)
-
Further, we need innovative new products to replace many of the products we use today. Living near Detroit I am of course familiar with the auto industry, and since early 2021 many manufacturers have committed to sell only electric vehicles in the coming decade. But the switch from petroleum to electric power will end millions of occupations, from the mechanical engineers and workers who develop and build engines, transmissions, coolant systems, and mufflers, to the auto service bays, the gas stations, and the oil drillers. New occupations will appear, in batteries, electric motors, integrated circuit development and software, but note the occupational changes, as the person who once repaired your engine is now tasked with designing software for a new circuit.
There is no more urgent task in developing a sustainable future than in continually upskilling the new workforce. Unfortunately, our academic systems are designed to suit the needs of the old workforce.
Lectures and readings can be found under 4IR Workforce.
New Methods of Teaching
Finally, in my opening lecture, I tell students that “nearly everyone gets an ‘A’ in my class”. I expect ‘A’ work and give them very freely. The caveats of the class are that you need to get the reading done on-time and contribute to the learning of others. Students will learn far more from each other than they will ever learn from me (but I get to choose the topics of conversation 😁).
I ‘flipped’ the class in response to the COVID-19 pandemic, reducing the number of and then recording the lectures and setting the weekly homework assignments to be short essays posted to a student-only forum. Students must post their own thoughts and respond to a few others, which is enough to start a conversation. For the synchronous session we continue that conversation in the Zoom or F2F sessions.
I’m interested in new methods of teaching, and will in the future post interesting links here.